Software Validation
Increasing product and system quality
Software Validation
Software Testing
Software Validation deals with various stages of Software testing activities such as
1. Static Testing
2. Software Unit Verification
3. Software Integration Testing
4. Functional Safety Validation
5. Model in Loop Testing
6. Test Automation (In-House Tools)
This white box testing is conducted for Automotive software products for Brakes, Suspension, and Steering & ADAS Business Units in order to satisfy ISO-26262 Functional safety standards. And also responsible for the development of Test Automation tools required to perform the similar testing jobs within the team.
Static Testing
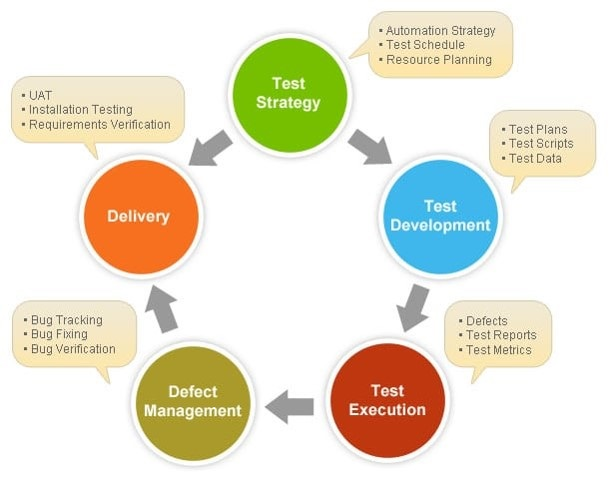
Testing is conducted to check the MISRA violations for the software products with the help of Industry certified tools to ensure the standard coding guidelines followed in the Software development activities.
Software Unit Verification

This software dynamic testing performed to verify the functionalities of software units & to verify implementation of the software w.r.t LLR (Low Level requirements).
Software Integration Testing
This software dynamic testing performed to verify the functionalities between various software Modules w.r.t SW Architectural Design Specifications.
Functional Safety Validation
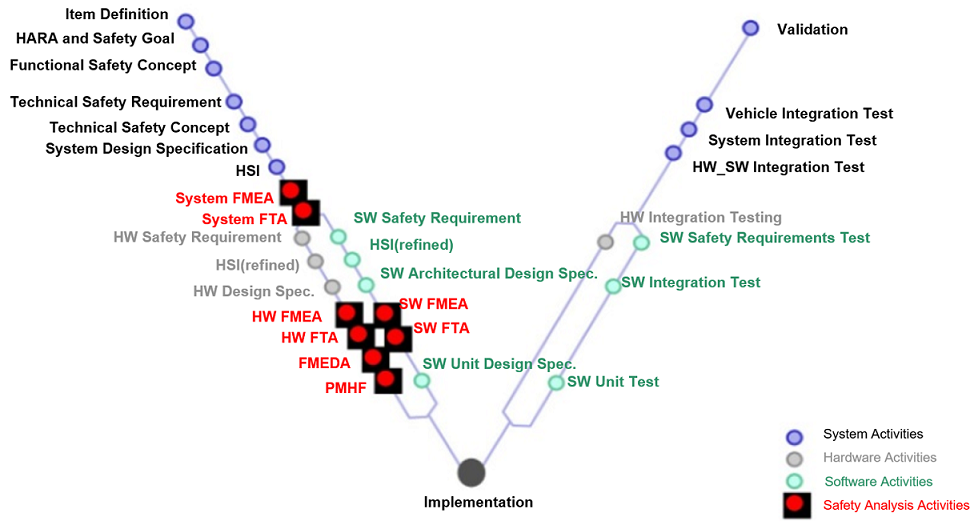
Functional Safety is a common part of the development process, Functional Safety Management Manual (FSMM) adapted in all HL Mando Automotive Products.
FSMM is applicable to the development of safety-related E/E systems to avoid unacceptable risk caused by malfunctioning behaviour of E/E systems. The FSMM aims to meet requirements on overall safety management in ISO-26262.
Model in Loop Testing
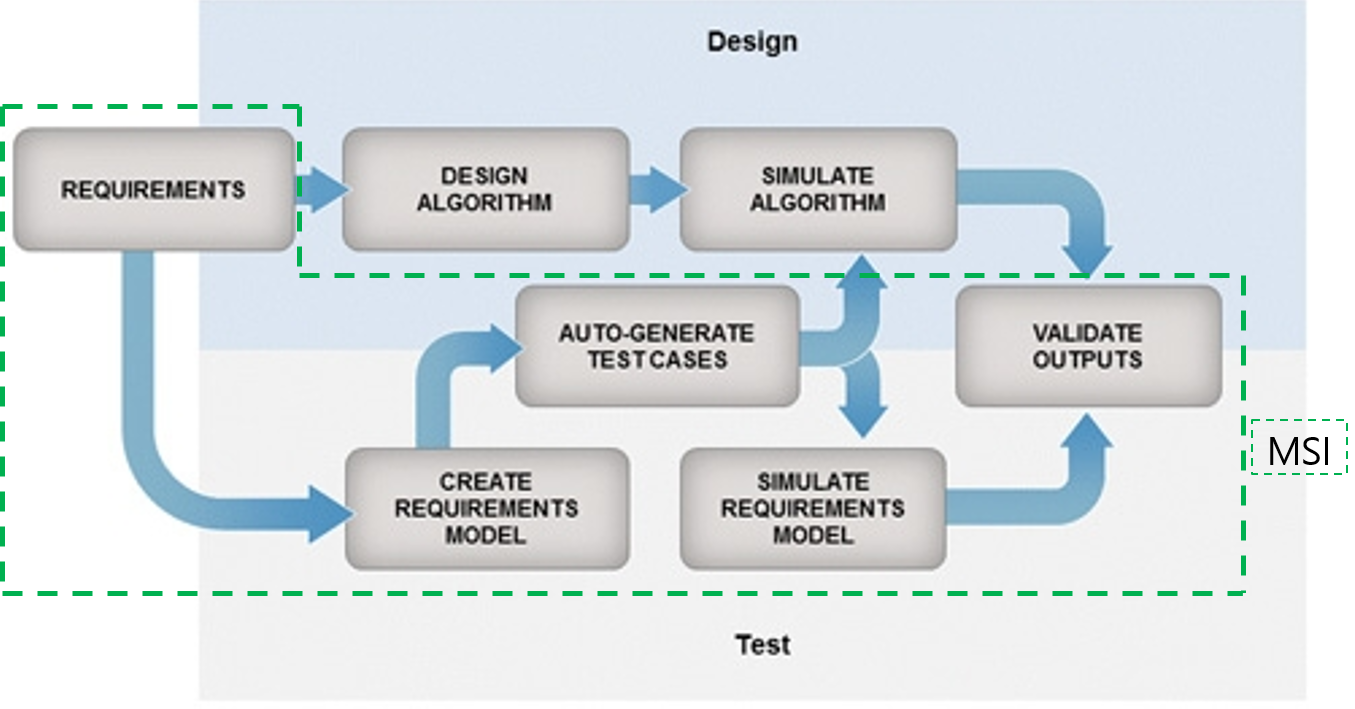
Model-in-the-loop testing (MIL) and simulation is a technique used to abstract the behaviour of a system or sub-system in a way that this model can be used to test, simulate and verify that model.
Test Automation (In-House Tools)
SW Validation team developed sample In house tools that helps testing teams to automate the certain testing activities.
Upcoming technology/ innovation
HL MSI SW validation emphasis to establish several other testing activities to stablish the software’s w.r.t Automotive safety standards
- Fault Injection Testing: In software testing, fault injection is a technique for improving the coverage of a test by introducing faults to test code paths, in particular error handling code paths that might otherwise rarely be followed.
- To extend the Software Dynamic testing at the target level eventually helps the Coding standards.
- Extension of MIL testing work to all the Software products across the other branches of HL Mando in globe.
- To perform the Functional safety activities by using the certified tools.
Software Function Test
Validation in HL MSI works towards improving ECU Software quality through various types of Sw qualification test which includes (CAN-Communication, Diagnostic, Failsafe, Data link layer, Network,Transport, Physical layer & Boot testing).
Our validation expertise include various products such as Brake, Steering, Suspension, OBC (On Board Charger), ADAS (Front camera, Front Range Radar, Short Range Radar).
Steering System
- System : C-EPS, R-EPS, DP-EPS & BN-EPS
- Diagnostics, Failsafe, Bootloader,CAN Communication test(Physical, Datalink, Network layer)
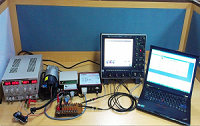
EPS Software Validation
System: DP-EPS (Dual Pinion Type Electric Power Steering)
DP-EPS is a steering system which uses an electric motor and ball nut reduction system rather than hydraulic pressure to provide steering assist. Reduced weight and improved efficiency ensure increased mileage/range. In addition, R-EPS provides proper steering and stability performance according to vehicle speed. R-EPS architecture is capable of performing autonomous driving like Automatic Parking, Lane Keep Assist (LKA) and Lane Follow Assist (LFA). Designed for medium vehicle platform

System: DP-EPS
System: BN-EPS (Ball-Nut Type Electric Power Steering)
BN-EPS is a fully electric power steering system for commercial vehicles, trucks, buses, etc. It uses energy only when necessary, which is different from hydraulic power steering systems which constantly consume energy to pressurize the system. The design increases fuel efficiency or range. In addition, it provides ADAS functions, improves safety and convenience to the driver.

System: BN-EPS
Flash Bootloader (FBL) Testing:
The bootloader is a SW component that resides in a permanent partition of the ECU's flash memory. The main purpose of the bootloader is to
- System : C-EPS, R-EPS
- Diagnostics, Failsafe, Bootloader,CAN Communication test(Physical, Datalink, Network layer)
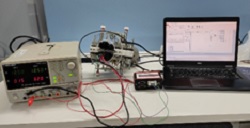
Flash Bootloader
Failsafe Testing:
A fail-safe is a design feature or practice that in the event of a specific type of failure, inherently responds in a way that will cause minimal or no harm to other equipment, to the system.
Diagnostic and Can Communication Testing:
In house testing of CAN standard (as per ISO 11898-1) Including physical layer and data-link layer implementations. With diagnostics testing as per UDS standard (ISO 14229-1) supported client-server model.
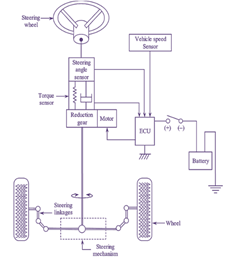
Diagnostic and Can Communication Testing
Brake System
- System: ABS, ESC, MOCi, IDB
- Diagnostics, Failsafe, Bootloader, CAN Communication test (Physical, Datalink, Network layer)
- New system: IDB2
- System level testing-Volvo SPA2
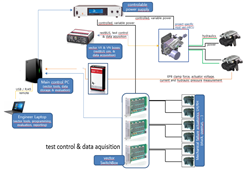
Brake System
Suspension
-
Flash Bootloader (FBL) Testing:
The Flash Bootloader (FBL) is an independent software module which enables embedded software download and any program module replacement which is part of ECU (it needs Flash or EEPROM memory).
-
Failsafe Testing:
A fail-safe is a design feature or practice that in the event of a specific type of failure, inherently responds in a way that will cause minimal or no harm to other equipment, to the environment or to people.
-
Diagnostic Testing
As per UDS standard (ISO 14229-1)
-
Can Communication Testing:
As per Standard ISO 11898-1 Including physical layer and data-link layer implementations.
-
NM Testing:
Its main purpose is to coordinate the transition between normal operation and bus-sleep mode of the network.
-
OTA Testing:
OTA is a technology to update the software or the firmware remotely.
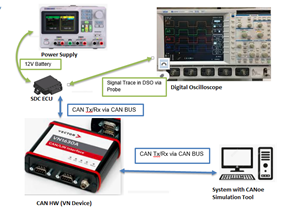
Suspension
Power Electronics: IDC,FDC,V2L,SBW,OBC/OBD
- The focus is on power conversion at the highest possible efficiency using very small control signals.
- Products: FCM 25/30, DCU 10/15/20,SRR 30
- Diagnostics, Failsafe, Bootloader, USM, Interface,CAN Communication test(Physical, Datalink, Network layer)
- FCM30 Functional Requirement Test
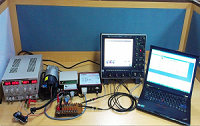
Power Electronics: IDC,FDC,V2L,SBW,OBC/OBD
Achievements & patents (USPTO, Korea PTO patent ID)
Title of Invention (Notice of Legal succession received) : Secure Bootloader with physical unclonable functionality : light weight, secure and very high performance bootloader Inventor: Aakanksha Kaushik (3800321) Patent Id: P2021-0363-KR
HILS System Test
Main work area of HILS team is to validate system ECUs. It validates the hardware and software with actual components. It provides virtual vehicle system for validating various real Conditions and real-time complex situation. HIL simulation will also allow tests that would normally destroy or damage the real system or vehicle. This is closely related to failure model and effects analysis.
With HIL simulation, the correct action of a control system to various failure modes can effectively be tested. This makes HIL simulation an effective technique to increase the safety of vehicle and systems. Using HILS simulation in an early stage of design phase, provide us a cost effective solution which can minimize the works in implementation phase and achieves the higher order of safety and stability of vehicle or system.
Brake HILS Test
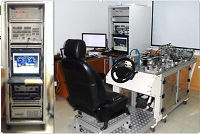
Brake HILS Test
- System Integration Test
- ABS/ESC/PBC/MOCi/IDB
- Performance Test
- Failsafe Test
- Value Added Function Test
EPS HILS Test
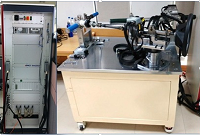
EPS HILS Test
- System Integration Test
- CEPS, REPS
- Performance Test
- Failsafe Test
- Value Added Function Test
Deepdive Diagnostic HILS Test

Deepdive Diagnostic HILS Test
- System Deepdive Diagnostic Test
- CEPS,REPS,EBS,PE,SUS
- ISO14229 protocol Test
- ISO15765 protocol Test
- Boot and Application Interface Test